What are dynamic work instructions?
In many operations, work instructions are paper documents. Each page describes a single step, and these pages are sorted and rearranged every time a new instruction sequence is needed to build a product.
During this process, instruction pages can often get lost, misplaced, or disorganized, resulting in lost time and product defects.
Digital work instructions can make managing instruction variations easy. We call this automatic, digital rearranging of different work instruction pages by work order dynamic work instructions.
Here is how dynamic work instructions with Tulip can help you simplify work instruction management.
First, here’s a video to help you understand the capabilities of our dynamic work instructions app:
Dynamic work instructions in action
There are two different main scenarios where dynamic work instructions can help. Which one you use will depend on the kinds of products you produce.
Large Variety of Products or Products with Varying Instructions
For products that are high-mix, work instructions can get complicated. With different products calling for different tasks and procedures, workers often have to flip through pages and pages of work instructions in different sequences. And these work instructions are not short. They can go up to a hundred pages. We’ve heard them referred to as “choose your own adventure” stories for assembly.
Here’s a quick example:
To build product A, a worker will use pages 3-8, 20-40, and then back to 5-9. For product B, the worker will use pages 20-30, 4-6, then 3-8.
Was that confusing to follow? Maybe you’re having flashbacks to flipping through massive work instruction packets yourself.
So what benefits do high-mix operations gain from using dynamic work instructions?
Benefits in High-Mix Operations
Truly Dynamic Work Instructions
Dynamic Digital Work Instructions allow you to manage complex procedures and tasks for hundreds and thousands of variations in products. You do not need to manually arrange tasks for each build or print out multiple pages of the same instructions for repeat tasks. Tulip allows you to create a ‘bank’ of tasks, pull them into sequences, and work up to building your final product. You can mix and match your tasks.
Catch all the Details of Production
Even the same products can have different variations. Upon pulling up the product order, dynamic work instructions can immediately identify the variations and display the correct order of tasks required to build that product. You can minimize any errors that come with manually rearranging work instructions. Dynamic work instructions let you work with confidence.
Visibility into Work Instructions Usage Data
Digital work instructions can track the time it takes to complete a single task or a sequence. You can see how many times the instructions were pulled, who used which instructions the most, and which instructions took the longest to complete. These data points can reveal whether workers need to be retrained or if the instructions need to be updated. You can measure how the real numbers stack up against the expected values.
Static Products
For shop floors making fixed inventory products at a high volume, dynamic work instructions may be most helpful when training new workers.
However, there are still many hidden benefits to digitizing work instructions, even for veteran workers that know every detail by heart.
Additional Benefits in Low-mix Shop Floors
Faster and Easier Work Instruction Update
Even the most static products need work instruction updates from time to time. Whether that change is adding one line of instructions to a task, adding an image, or removing a task entirely, digital instructions make it much more accessible to edit and deploy.
Digital work instructions can shorten the manual editing → printing → replacing → redeployment process to editing → deployment.
With a few simple clicks, you can update and harmonize all of your work instructions to the most current version.
Minimize Errors
No matter how skilled and trained the workers are, mistakes still happen. By digitizing instructions and assigning each task to a worker, you can truly error-proof the production process by confirming that each task is accurately completed. It allows workers to double-check their work.
Better Training
When onboarding new workers, ensure that they have gone through proper training by having them digitally sign off when they go through instructions. Dynamic work instructions can ensure that new workers receive appropriate training.
Other Benefits: Management
It is obvious that dynamic work instructions benefit operators. But they can also create transparency across the organization, allowing visibility into progress, training, and the bottlenecks. The management can assess the data on how long tasks take, the lead time, and cycle time and use it to improve shop floor performance and processes. The training data can also be used to improve the onboarding process when new workers join. Overall, dynamic work instructions give management the opportunity to achieve continuous improvement and optimization.
How Tulip works for DWI
If you haven’t already, you might want to watch the video explaining how Tulip’s dynamic work instruction app can streamline the product-building process.
But here is another breakdown of our app’s capabilities and how you can gain all the benefits we have listed above.
WI Builder: Work Up to Your Instructions
Dynamic work instructions are built out of three basic building blocks:
- Tasks
- Procedures
- Routings
Task – A task is a step. It’s a single action an operation might perform. Traditionally, this would be a single page in a work instruction packet. In Tulip, it’s a single screen.
Procedure – A procedure is a group of tasks. Many product variations will call for a consistent ordering of different tasks. By creating procedures, you can create large units for organizing your work instructions.
Routings – Routings are specific orderings of tasks and procedures. After you create and store your various activities, you set the different sequences for product variations. Your apps then automatically route those building blocks into complete work instructions.
Work Instructions App walkthrough
Our customer success lead Sarah is a killer baker. Since operations products are so different, she thought she could best communicate how DWIs work by making an app to organize her cake recipes.
Here’s what a single step from one of her work instructions looks like:
1. Manage Tasks
In the task manager, Sarah creates a sequence of tasks that go into a cake. For every “cake” or product variation, you create that ordering out of tasks in your library.
For any task, you can add instructions, images, quality checks, and more. Here is what that task editor looks like:
2. Manage Procedure
In our example, baking the cake and applying the icing are two different procedures. Sarah bakes a bunch of different cakes and uses many different icings. There are tons of combinations. Each has to be prepared following its own set of instructions. For any giving cake, she needs to be able to pull the right instructions for the base and icing.
Here is the procedure manager that lets you group and order tasks to build parts of a final product. Notice how you can add the same task twice if the step reoccurs in the procedure.
3. Manage Routing
Routing is the final step. A routing will pull the right set of procedures and tasks for the project at hand.
Here, it’s a chocolate cake with chocolate icing.
4. Implementing DWI
Once you have set up the tasks, procedures, and routings, it is now time to create a job and assign it to a worker.
Just because the routing has been configured does not mean that the product is ready for production. You need to create a job associated with that routing to push it to production.
Job is the work order. If you want to make 20 chocolate layered cakes, you can create 20 jobs of the same configuration. If the 20 jobs are for 20 separate birthdays, you can also change the name of each job in the JobID as well.
Conclusions
In this use case, we’ve covered:
- Different use case scenarios with Tulip
- Guide to using our dynamic work instructions app
- Benefits of using our dynamic work instructions app
Build Dynamic Work Instructions with Tulip's Frontline Operations Platform
See how a system of apps can guide operators and capture real-time production data with a free trial of Tulip.
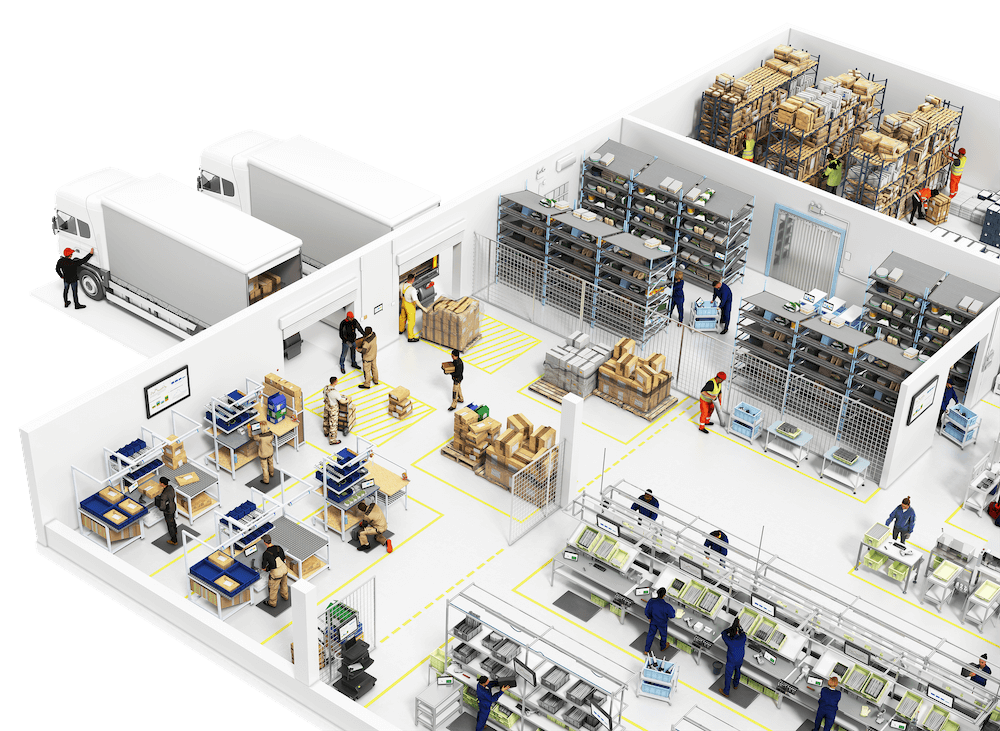