What is Total Quality Management?
Total Quality Management (TQM) is a framework revolving around the principle that quality needs to be maintained in every aspect of a company’s operations.
This means that everyone in the organization is accountable for the quality of the output, leading to fewer errors and continual improvement of operations. Simply put, the end goal of TQM is doing the right things, right the first time, every time.
What are the Principles of TQM?
There are 8 key principles of TQM that help guide strategy and activities throughout an organization.
- Customer focus
- Total employee commitment
- Process-oriented thinking
- Integrated systems
- Quality as a strategy
- Continuous Improvement
- Fact-based decision making
- Effective communication
Let’s look at each more closely.
Customer Focus: Understand your customers’ needs. After all, they are the ultimate decision-makers on whether or not your product meets quality standards.
Total Employee Commitment: Everyone in the organization is responsible for their part of producing a quality product. Empower employees through training and recognition, and give them the tools they need to reach and exceed goals.
Process-Centered: Ensure consistency by defining clear processes across the organization. This involves evaluating current processes, identifying bottlenecks and areas for improvement, and making sure performance is continuously monitored.
Integrated System: Functions within organizations are often siloed. In TQM, information should also flow horizontally across the organization. Everyone should understand how their role fits in with the organization’s goals.
Strategic Approach: Quality should be a core component of the organization’s strategy. This involves a commitment to a plan, deploying the plan, reviewing the plan, and continually improving it.
Continuous Improvement: There should always be a focus on finding ways to continually improve processes to adapt to customer needs or increase efficiency.
Fact-Based Decision Making: Use a data-driven approach to make decisions and predictions. Collecting and analyzing data regularly will allow you to make informed decisions based on reality.
Effective Communication: So much of TQM revolves around an entire organization’s commitment to quality. Employees should establish clear lines of communication, be involved in decision-making, and receive regular feedback and updates.
How Does TQM Improve Quality?
You might have read all those principles and wondered, but what do all of those principles really mean for your factory, and how do they improve quality?
In manufacturing, using a TQM approach ensures that internal practices are set up to reduce errors and streamline processes.
While an approach like Six Sigma looks at reducing defects through a methodological process, TQM focuses on combining people and processes to reduce errors. It takes a preventative approach to quality, usually through error-proofing or early error detection.
Poka Yoke
Poka-Yoke means “error-proofing” a process by catching, correcting, and eliminating mistakes at the source. For example, in daily life, spell-checking functions prevent us from making mistakes before we have a chance to send out misspelled communications. In manufacturing, implementing poka-yoke can prevent processing errors, setup errors, measurement errors, and more.
Early Detection
Even if you error-proof your processes, there may be mistakes that fall through the cracks. At this stage, it’s important that you can detect errors early before they move downstream. For example, you could add inline quality checks at different stages of production, especially when there is a hand-off step in a process when output is transferred to another worker.
Conclusion
Implementing TQM takes participation from everyone, from top management to operators on the shop floor. While top management needs to educate everyone on TQM principles, set overarching goals, and oversee the effort, it is the frontline workforce that has deep knowledge of existing manufacturing processes and how to improve them. It is truly up to everyone to create a TQM culture.
Eliminate the source of product defects and reduce your cost of quality with Tulip
Reduce the cost of scrap and rework with apps that help digitize workflows, automate data collection, and improve production efficiency.
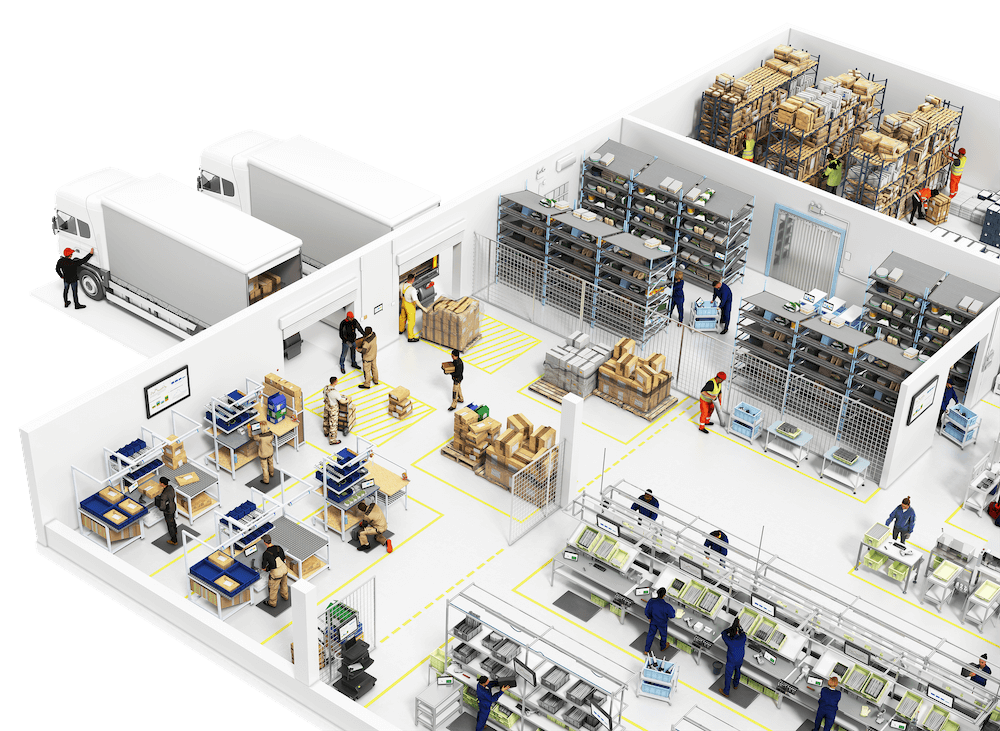