Line Balancing in Manufacturing Defined
Line balancing is a production strategy that involves balancing operator and machine time to match the production rate to the takt time.
Takt time is the rate at which parts or products must be produced in order to meet customer demand.
For a given production line, if production time is exactly equal to takt time, then the line is perfectly balanced. Otherwise, resources should be reallocated or rearranged to remove bottlenecks or excess capacity. In other words, the quantities of workers and machines assigned to each task in the line should be rebalanced to meet the optimal production rate.
Benefits of Line Balancing
1. Reduce waiting waste
Waiting waste is one of the 8 types of waste of Lean manufacturing. It refers to any idle time that occurs when operations are not fully synchronized. For example, waiting waste occurs when operators are waiting for materials or for someone else to complete their task. Equipment downtime–time during which equipment is not operating–is another example of waiting waste.
Line balancing ensures that all operators and machines work together in a balanced fashion. No operator or machine should be overburdened or idle. By minimizing downtime, line balancing reduces waiting waste.
2. Reduce inventory waste
Inventory waste is another type of waste. It corresponds to an excess of raw materials, work in progress (unfinished goods), or finished goods. Inventory waste indicates the inefficient allocation of capital.
Line balancing standardizes production, meaning it is much easier to avoid build-ups or surplus inventory. By reducing idle time, line balancing ensures that there is minimum work in progress. And finally, by bringing production time closer to takt time, it guarantees on-time delivery.
3. Absorb internal and external irregularities
Line balancing reduces variations within a production line. A balanced production line is stable and flexible enough to adapt to changes.
For example, if customer demand changes–meaning takt time changes–operations can be realigned quickly through line balancing. The consequences of changes brought to a balanced production line are predictable. It is thus much easier to modify the line to adjust the production rate.
4. Reduce production costs and increase profits
Perfect line balancing leads to workers and machines that perform in a fully synchronized manner. No operator is paid for standing idle. All machines are used to their full potential. In other words, manpower and machine capacity are maximized. Such process efficiency represents fewer costs and more profits.
How can you achieve line balancing?
1. Calculate takt time
Since the goal of line balancing is to match the production rate to takt time, being aware of your takt time is essential. Tulip offers an out-of-the box Takt Time App and Takt Time Dashboard that make calculating and tracking takt time a seamless part of your production process.
2. Perform time studies
We wrote a detailed article on how to conduct time studies. The goal of time studies is to establish the time required to complete each task along a production line. In other words, you want to find out how long employees and machines spend on each part of a process.
Keep in mind that while it is possible to do time studies with a stopwatch and clipboard, there are now significantly better options. IoT connectivity and cloud computing have transformed data collection and storage. With sensors and manufacturing apps, manufacturers can now perform automatic and continuous time studies, thus eliminating human bias and sample size effect.
3. Identify bottlenecks and excess capacity
When it comes time to analyze the data from your time studies, notice which parts of the process are taking longer than takt time. Exceeding takt time means late deliveries, high shipping costs or unhappy customers. Also, notice which parts are taking less than takt time. There is excess capacity in those places.
4. Reallocate resources
Start by considering task precedence, which is the sequence in which tasks must be carried out. For example, if a step requires a certain part, you need to make sure that part is completed before reaching that step. A Precedence Diagram can come in handy.
Then, rearrange tasks to reduce excess capacity and bottlenecks. For example, move resources–workers and equipment–from parts of the line that have excess capacity to bottlenecks. In other words, aim to alleviate the workload where there are blockages, and move it to places where excess capacity can be filled by absorbing more work. This will reduce the waiting waste in the places where there was excess capacity. It will also help improve production flow where there were bottlenecks.
Try to organize elementary tasks into groups that minimize operators’ idle time and that maximize the utilization of machines and equipment. Share the workload among operators in the most logical way, taking into account the data on operator performance that you have gathered. Ideally, each group of tasks should be completed in the same amount of time to achieve synchronization.
Consider if you have too many or too few workstations. Line balancing might improve process efficiency to a point where there is excess capacity throughout your line. It might be beneficial to remove workstations or combine processes.
Wherever you have several operators performing consecutive tasks and working as a unit, you should strive to reduce the imbalance between workers and workloads. Proper arrangement and allocation of tasks in production lines help maximize output at the desired time.
5. Make other improvements
The analysis of the quantitative data on your lines will surely reveal other opportunities for improvement that could improve the balance of your lines.
To implement process improvement, you can manipulate three parameters: operator time, machine time, and setup time. For instance, you can give additional training to workers that take longer to complete tasks or facilitate transitions to reduce changeover times. You can also upgrade machines or make sure operators follow proper machine setup and maintenance standard operating procedures (SOPs).
Many Lean practices can also help reduce variation in your lines. 5S and visual management create a coherent workspace, thus reducing the time wasted looking for tools and improving process efficiency. Poka-yoke, or error-proofing, a process that helps catch defects early, which increases the consistency of output.
Conclusions
Line balancing is an optimization problem with significant industrial importance. By improving the efficiency of their lines, organizations can reduce the wastes of Lean manufacturing and unlock more value.
Improve productivity across your operations with Tulip
Learn how you can reduce waste and increase production efficiency with no-code, industrial applications.
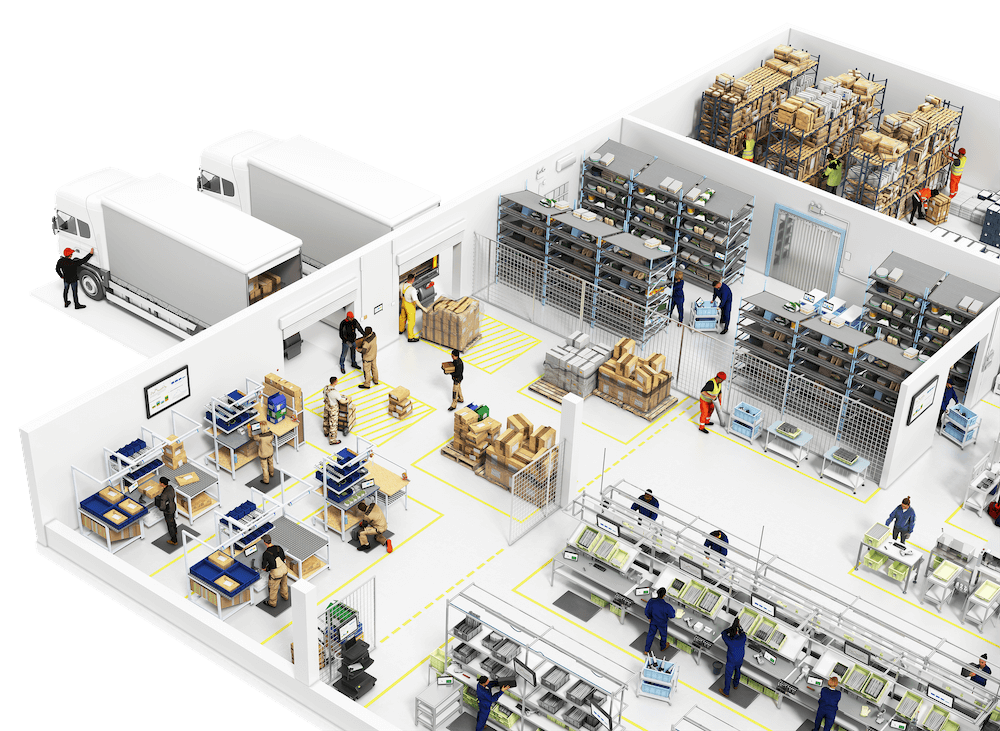