En el entorno de trabajo cada vez más digital de hoy en día, los fabricantes están invirtiendo considerablemente en diversas máquinas y dispositivos para complementar los flujos de trabajo de los operarios en el taller.
Este auge de la fábrica conectada se ha visto facilitado por el creciente desarrollo del internet industrial de las cosas (IIoT). Estas máquinas, dispositivos y sensores habilitados para internet transfieren datos entre ellos y otros sistemas asociados, conectando toda la planta de producción.
A medida que el sitio web industrial IoT ha ido madurando en los últimos años, las empresas están produciendo más datos que nunca. Como resultado, la necesidad de que los datos viajen de forma rápida, eficiente y segura a los sistemas y centros de datos relacionados ha crecido significativamente.
Las pasarelas industriales IoT ayudan a facilitar esta transferencia puntual de datos, acercando la potencia de procesamiento a la fuente de datos: las máquinas en el taller.
Las pasarelas y los dispositivos relacionados permiten a los fabricantes dar más sentido a los datos recopilados. Y lo que es más importante, el análisis de los datos se produce con mayor rapidez, lo que proporciona a los responsables de la toma de decisiones una visión rápida y les permite aplicar soluciones.
En este post, exploraremos las pasarelas industriales IoT y su importancia a la hora de conectar las máquinas y los dispositivos que alimentan el taller.
¿Qué es una pasarela industrial IoT ?
Una pasarela industrial IoT es un dispositivo instalado en el taller para conectar y recopilar datos de varias máquinas industriales y dispositivos IoT .
Una vez recopilados, la pasarela IoT reenvía estos datos a la nube o a los centros de datos para su procesamiento, supervisión y control remotos, así como un análisis más profundo.
IoT puertas de enlace frente a dispositivos de borde
Aunque los fabricantes han confiado durante mucho tiempo en las pasarelas de IoT para conectar y transferir datos a los centros de procesamiento o a la nube, el auge de la computación de borde ha presentado nuevas oportunidades para las empresas que buscan procesar datos de forma más rápida y eficiente.
En primer lugar, hay muchas pasarelas IoT que permiten la computación en el borde, pero la mayoría de las pasarelas IoT tradicionales no lo hacen.
Uno de los retos de las pasarelas tradicionales de IoT es que el gran volumen de datos que producen los dispositivos requiere conexiones más complejas y costosas con los centros de almacenamiento y procesamiento de datos. Con los dispositivos de borde, los datos pueden almacenarse localmente y transferirse a la nube o a centros de procesamiento locales a través de conexiones menos costosas, incluso a través de Internet.
Además, la naturaleza del trabajo que realizan los dispositivos de IoT ha evolucionado hasta crear la necesidad de una transferencia más inmediata de datos entre dispositivos.
Con las pasarelas tradicionales de IoT , suele haber cierta latencia en la transferencia de datos entre las máquinas, los dispositivos o los sensores y la nube o los centros de datos. Con los dispositivos de borde, en cambio, los datos pueden almacenarse y procesarse en el borde, eliminando la latencia debida a la transferencia y el procesamiento de datos a larga distancia.
Aunque su función es similar, las ventajas de la computación de borde incluyen un tiempo de respuesta más rápido para las aplicaciones que lo requieren y una menor necesidad de conexiones de largo recorrido a los centros de procesamiento y almacenamiento.
Recopile datos en tiempo real de todas sus operaciones
Aprenda cómo el conjunto de dispositivos de borde de Tulip puede ayudarle a conectar máquinas y dispositivos IoT en todas sus operaciones.
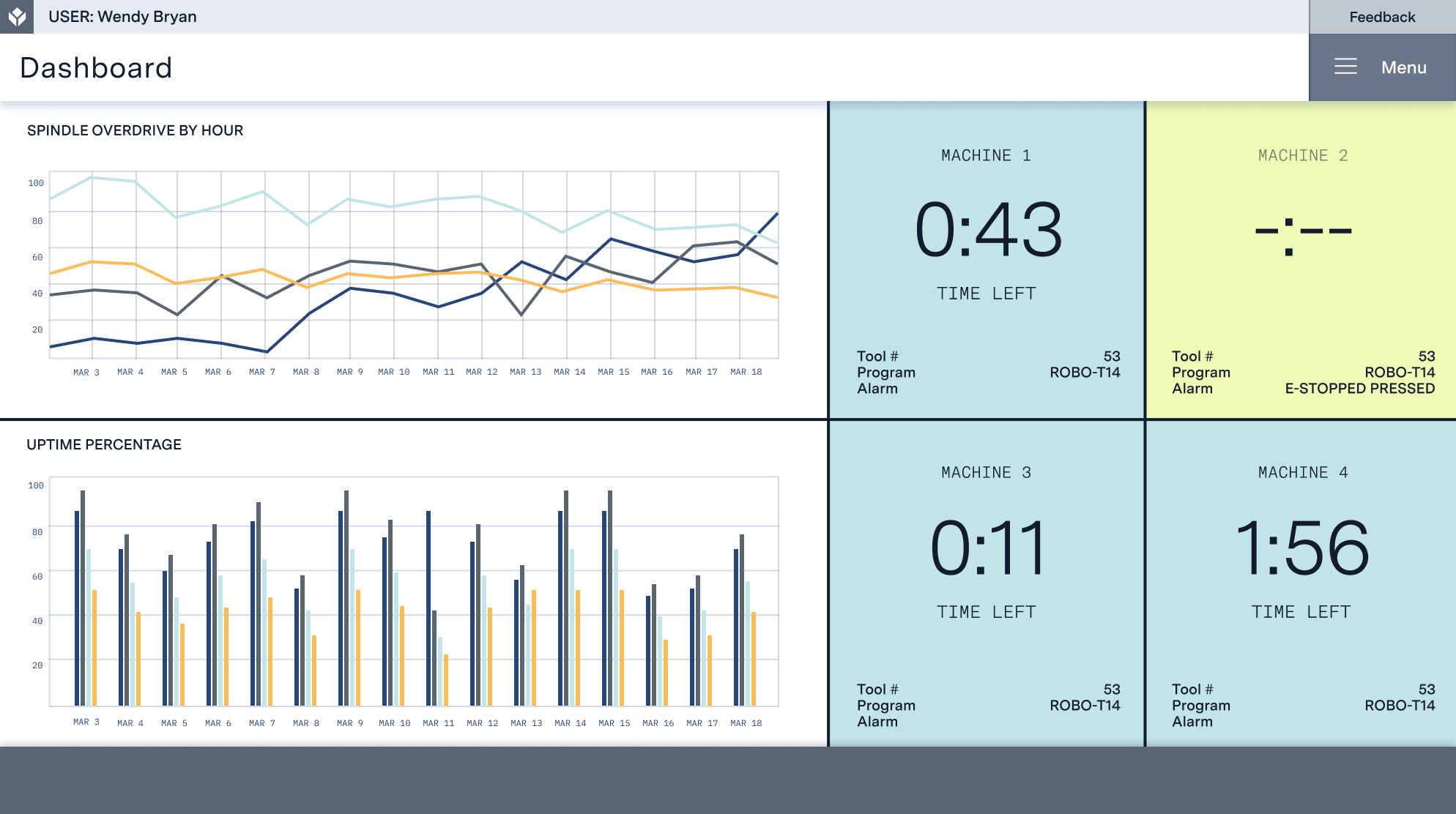
La importancia de las pasarelas IIoT
Las pasarelas de dispositivos industriales IoT son vitales para el buen funcionamiento de las operaciones de fabricación modernas. Son importantes en los siguientes aspectos:
Conectividad entre dispositivos y recopilación de datos: Los fabricantes utilizan pasarelas para establecer un puente entre sus sistemas heredados y las máquinas y equipos del taller. Como resultado, los fabricantes pueden recopilar datos de sus máquinas avanzadas, así como de los sistemas heredados.
Esto permite a los fabricantes supervisar las métricas de las máquinas de distintas generaciones tecnológicas. Además, las pasarelas IIoT unen máquinas con diferentes protocolos, fomentando la interoperabilidad para una comunicación eficiente.
Además, estos dispositivos reducen la latencia en las redes al procesar los datos en bruto. Esto mejora la velocidad, la fiabilidad y la flexibilidad durante la recogida y la transferencia de datos.
Procesamiento de datos en tiempo real para la toma de decisiones: Las pasarelas IoT conectadas al borde procesan y analizan los datos en la fuente en tiempo real. De este modo, las pasarelas eliminan la necesidad de transferir los datos a través de largas distancias a un centro de datos para su procesamiento y análisis. Esto permite el análisis en tiempo real, fomentando la toma de decisiones a tiempo.
Supervisión de la producción: Dado que las pasarelas IoT recopilan y procesan los datos en tiempo real, los fabricantes obtienen una visibilidad completa y puntual de los procesos de producción. Como resultado, los supervisores y gerentes pueden vigilar las tiradas de producción, obteniendo instantáneas precisas del proceso de producción en cualquier momento y fase.
Supervisión del estado de las máquinas y mantenimiento predictivo: Los fabricantes utilizan pasarelas industriales IoT y sensores habilitados para IoT para realizar un seguimiento del rendimiento de cada máquina. Estos dispositivos supervisan los parámetros de salud de las máquinas, proporcionando información en tiempo real sobre su rendimiento.
A continuación, estos datos pueden pasarse a un sistema digital que puede procesarlos y analizarlos automáticamente, proporcionando a los equipos de mantenimiento información que indique un posible fallo de la máquina. Esto permite al equipo ejecutar un mantenimiento predictivo, reduciendo significativamente el tiempo de inactividad en el taller.
Ventajas de las pasarelas IoT conectadas al borde
Los fabricantes modernos utilizan las pasarelas IIoT para optimizar diversas partes del proceso de producción. La instalación de estas pasarelas proporciona varios beneficios a los fabricantes que buscan aprovechar la potencia del Internet industrial de las cosas. Algunos de estos beneficios incluyen:
Velocidades de comunicación de dispositivos más rápidas: Como ya se ha comentado, muchas pasarelas modernas de IoT son capaces de almacenar y procesar datos en el borde. Como resultado, eliminan la latencia y pueden responder a las acciones que tienen lugar en el taller en tiempo real.
Rápida adición y configuración de dispositivos: Para muchos fabricantes, añadir y configurar dispositivos puede resultar todo un reto. Sin embargo, las modernas pasarelas industriales IoT tienen capacidades plug-and-play, utilizando aplicaciones sin código para añadir y configurar diversas máquinas y sensores del taller.
Seguridad robusta: las pasarelas de dispositivos de IIoT están equipadas con potentes cortafuegos industriales, que separan la maquinaria de fabricación de Internet. Esto protege los activos de producción de los malos actores, garantizando la integridad de los datos.
Reducción de los costes de explotación: las pasarelas IIoT reducen los costes de explotación de varias maneras. Por ejemplo, los dispositivos permiten la supervisión en tiempo real de las máquinas y los sensores, identificando posibles tiempos de inactividad y permitiendo a los trabajadores responder y solucionar los problemas rápidamente. De este modo, la producción continua garantiza el cumplimiento y la entrega puntual de los pedidos.
Además, las empresas manufactureras gastan menos en ancho de banda de red. Al fin y al cabo, las pasarelas procesan los datos en bruto, comprimiéndolos para que ocupen menos ancho de banda, como ya se ha comentado.
Una visión general de Tulip's Edge IO
Como hemos comentado, la capacidad de recopilar y procesar datos de producción en el borde puede ser increíblemente poderosa para los fabricantes que buscan supervisar sus máquinas, dispositivos y sensores.
Tulip ofrece dos dispositivos de borde que permiten a los fabricantes conectar y configurar sus equipos con nuestra plataforma de operaciones sin código. Con nuestro Edge MC y Edge IOlos fabricantes pueden recopilar datos de máquinas analógicas y personalizadas con sensores o cámaras, así como de máquinas en red con soporte nativo para OPC UA, así como una variedad de protocolos populares a través de Node-RED.
Además, nuestros dispositivos de borde son rentables, fáciles de configurar y pueden utilizarse para una gran variedad de casos de uso. Esto favorece la mejora continua, la escalabilidad y produce un tiempo de obtención de valor sin precedentes.
Si está interesado en saber cómo Tulip puede ayudarle a obtener información de las máquinas, sensores y dispositivos de todas sus operaciones, póngase en contacto con un miembro de nuestro equipo hoy mismo¡!
Conecte sus máquinas y dispositivos IIoT
Aprenda cómo puede utilizar la plataforma y los dispositivos de Tulip para recopilar datos en tiempo real de todas sus operaciones.