Linienbalancierung in der Fertigung Definiert
Line Balancing ist eine Produktionsstrategie, bei der die Bediener- und Maschinenzeiten so aufeinander abgestimmt werden, dass die Produktionsrate mit der Taktzeit übereinstimmt.
Die Taktzeit ist die Geschwindigkeit, mit der Teile oder Produkte produziert werden müssen, um die Kundennachfrage zu erfüllen.
Wenn bei einer bestimmten Produktionslinie die Produktionszeit genau der Taktzeit entspricht, dann ist die Linie perfekt ausbalanciert. Andernfalls sollten die Ressourcen umverteilt oder neu angeordnet werden, um Engpässe oder Überkapazitäten zu beseitigen. Mit anderen Worten: Die Mengen an Arbeitern und Maschinen, die jeder Aufgabe in der Linie zugewiesen sind, sollten neu ausbalanciert werden, um die optimale Produktionsrate zu erreichen.
Vorteile von Line Balancing
1. Verringern Sie Wartezeitabfälle
Wartende Abfälle sind eine der 8 Abfallarten von Lean manufacturing. Sie bezieht sich auf alle Leerlaufzeiten, die entstehen, wenn die Arbeitsabläufe nicht vollständig synchronisiert sind. Wartezeit entsteht zum Beispiel, wenn Mitarbeiter auf Material warten oder darauf, dass jemand anderes ihre Aufgabe erledigt. Ein weiteres Beispiel für Verschwendung durch Warten ist die Zeit, in der die Geräte nicht in Betrieb sind.
Der Linienausgleich stellt sicher, dass alle Bediener und Maschinen in einem ausgewogenen Verhältnis zusammenarbeiten. Kein Bediener und keine Maschine sollte überlastet oder untätig sein. Durch die Minimierung der Stillstandszeiten reduziert das Line-Balancing die Wartezeitverschwendung.
2. Reduzieren Sie Inventarverschwendung
Eine weitere Art von Verschwendung ist die Verschwendung von Lagerbeständen. Sie entspricht einem Überschuss an Rohstoffen, unfertigen Erzeugnissen (unfertige Waren) oder Fertigerzeugnissen. Die Verschwendung von Lagerbeständen ist ein Zeichen für die ineffiziente Allokation von Kapital.
Durch das Line Balancing wird die Produktion standardisiert, so dass es viel einfacher ist, Anhäufungen oder überschüssige Bestände zu vermeiden. Durch die Verringerung der Leerlaufzeiten stellt das Linientuning sicher, dass nur ein Minimum an unfertiger Arbeit vorhanden ist. Und schließlich wird durch die Annäherung der Produktionszeit an die Taktzeit eine pünktliche Lieferung garantiert.
3. Interne und externe Unregelmäßigkeiten absorbieren
Der Linienausgleich reduziert die Schwankungen innerhalb einer Produktionslinie. Eine ausgeglichene Produktionslinie ist stabil und flexibel genug, um sich an Veränderungen anzupassen.
Wenn sich zum Beispiel die Kundennachfrage ändert - d.h. die Taktzeit -, kann der Betrieb schnell durch einen Linienabgleich neu ausgerichtet werden. Die Folgen von Änderungen an einer ausbalancierten Produktionslinie sind vorhersehbar. Es ist daher viel einfacher, die Linie zu modifizieren, um die Produktionsrate anzupassen.
4. Senkung der Produktionskosten und Steigerung der Gewinne
Perfekte Linienbalancierung führt zu Arbeitern und Maschinen, die vollständig synchronisiert arbeiten. Kein Arbeiter wird für Untätigkeit bezahlt. Alle Maschinen werden mit ihrem vollen Potenzial genutzt. Mit anderen Worten, die Arbeitskraft und die Maschinenkapazität werden maximiert. Eine solche Prozesseffizienz bedeutet weniger Kosten und mehr Gewinn.
Wie können Sie den Zeilenausgleich erreichen?
1. Berechnen Sie die Taktzeit
Da das Ziel der Abtaktung darin besteht, die Produktionsrate an die Taktzeit anzupassen, ist es wichtig, die Taktzeit zu kennen. Tulip bietet eine sofort einsatzbereite Taktzeit-App und ein Dashboard, die die Berechnung und Verfolgung der Taktzeit zu einem nahtlosen Teil Ihres Produktionsprozesses machen.
2. Zeitstudien durchführen
Wir haben einen ausführlichen Artikel darüber geschrieben , wie man Zeitstudien durchführt. Das Ziel von Zeitstudien ist es, die Zeit zu ermitteln, die für die Erledigung der einzelnen Aufgaben entlang einer Produktionslinie benötigt wird. Mit anderen Worten: Sie wollen herausfinden, wie viel Zeit Mitarbeiter und Maschinen für jeden Teil eines Prozesses aufwenden.
Denken Sie daran, dass es zwar möglich ist, Zeitstudien mit einer Stoppuhr und einem Klemmbrett durchzuführen, aber es gibt jetzt wesentlich bessere Möglichkeiten. IoT Konnektivität und Cloud Computing haben die Datenerfassung und -speicherung verändert. Mit Sensoren und Fertigungs-Apps können Hersteller jetzt automatische und kontinuierliche Zeitstudien durchführen und so menschliche Verzerrungen und den Effekt der Stichprobengröße eliminieren.
3. Identifizieren Sie Engpässe und Überkapazitäten
Wenn es an der Zeit ist, die Daten aus Ihren Zeitstudien zu analysieren, achten Sie darauf, welche Teile des Prozesses länger als die Taktzeit dauern. Eine Überschreitung der Taktzeit bedeutet verspätete Lieferungen, hohe Versandkosten oder unzufriedene Kunden. Achten Sie auch darauf, welche Teile weniger als die Taktzeit benötigen. An diesen Stellen gibt es Überkapazitäten.
4. Ressourcen neu zuteilen
Denken Sie zunächst an die Priorität der Aufgaben, d.h. an die Reihenfolge, in der die Aufgaben ausgeführt werden müssen. Wenn beispielsweise für einen Schritt ein bestimmter Teil erforderlich ist, müssen Sie sicherstellen, dass dieser Teil abgeschlossen ist, bevor Sie diesen Schritt erreichen. Ein Prioritätsdiagramm kann hier sehr hilfreich sein.
Dann ordnen Sie die Aufgaben neu an, um Überkapazitäten und Engpässe abzubauen. Verlegen Sie beispielsweise Ressourcen - Mitarbeiter und Ausrüstung - von Teilen der Linie, die Überkapazitäten aufweisen, zu Engpässen. Mit anderen Worten: Versuchen Sie, die Arbeitslast dort zu verringern, wo es Blockaden gibt, und sie dorthin zu verlagern, wo überschüssige Kapazitäten durch die Aufnahme von mehr Arbeit gefüllt werden können. Auf diese Weise wird die Wartezeit an den Stellen, an denen Überkapazitäten bestehen, verkürzt. Es wird auch dazu beitragen, den Produktionsfluss dort zu verbessern, wo es Engpässe gab.
Versuchen Sie, elementare Aufgaben in Gruppen zu organisieren, die die Leerlaufzeit der Bediener minimieren und die Auslastung der Maschinen und Geräte maximieren. Verteilen Sie das Arbeitspensum unter den Bedienern auf die logischste Weise und berücksichtigen Sie dabei die Daten über die Leistung der Bediener, die Sie gesammelt haben. Idealerweise sollte jede Gruppe von Aufgaben in der gleichen Zeit erledigt werden, um eine Synchronisierung zu erreichen.
Überlegen Sie, ob Sie zu viele oder zu wenige Arbeitsstationen haben. Durch einen Linienausgleich kann die Prozesseffizienz bis zu einem Punkt verbessert werden, an dem es in Ihrer gesamten Linie Überkapazitäten gibt. Es könnte von Vorteil sein, Arbeitsplätze abzubauen oder Prozesse zusammenzulegen.
Wo immer Sie mehrere Bediener haben, die aufeinanderfolgende Aufgaben ausführen und als Einheit arbeiten, sollten Sie sich bemühen, das Ungleichgewicht zwischen Arbeitern und Arbeitsbelastung zu verringern. Die richtige Anordnung und Zuteilung von Aufgaben in Produktionslinien trägt dazu bei, den Output zum gewünschten Zeitpunkt zu maximieren.
5. Andere Verbesserungen vornehmen
Die Analyse der quantitativen Daten zu Ihren Linien wird sicherlich weitere Verbesserungsmöglichkeiten aufzeigen, die die Bilanz Ihrer Linien verbessern könnten.
Um Prozessverbesserungen durchzuführen, können Sie drei Parameter beeinflussen: Bedienerzeit, Maschinenzeit und Einrichtungszeit. Sie können zum Beispiel zusätzliche Schulungen für Mitarbeiter anbieten, die länger für die Erledigung von Aufgaben brauchen, oder Übergänge erleichtern, um die Umrüstung Zeiten zu verkürzen. Sie können auch Maschinen aufrüsten oder sicherstellen, dass die Bediener die Standardarbeitsanweisungen (SOPs) für die Einrichtung und Wartung der Maschinen befolgen.
Viele Lean-Praktiken können auch dazu beitragen, Abweichungen in Ihren Produktionslinien zu reduzieren. 5S und visuelles Management schaffen einen kohärenten Arbeitsbereich, wodurch weniger Zeit mit der Suche nach Werkzeugen verschwendet wird und die Prozesseffizienz verbessert wird. Poka-yoke oder Fehlersicherung, ein Prozess, der dazu beiträgt, Fehler frühzeitig zu erkennen, was die Konsistenz der Produktion erhöht.
Schlussfolgerungen
Der Ausgleich von Produktionslinien ist ein Optimierungsproblem mit großer industrieller Bedeutung. Indem sie die Effizienz ihrer Linien verbessern, können Unternehmen die Verschwendung von Lean manufacturing reduzieren und mehr Wert freisetzen.
Verbessern Sie die Produktivität Ihres gesamten Betriebs mit Tulip
Erfahren Sie, wie Sie mit no-code, industriellen Anwendungen Abfall reduzieren und die Produktionseffizienz steigern können.
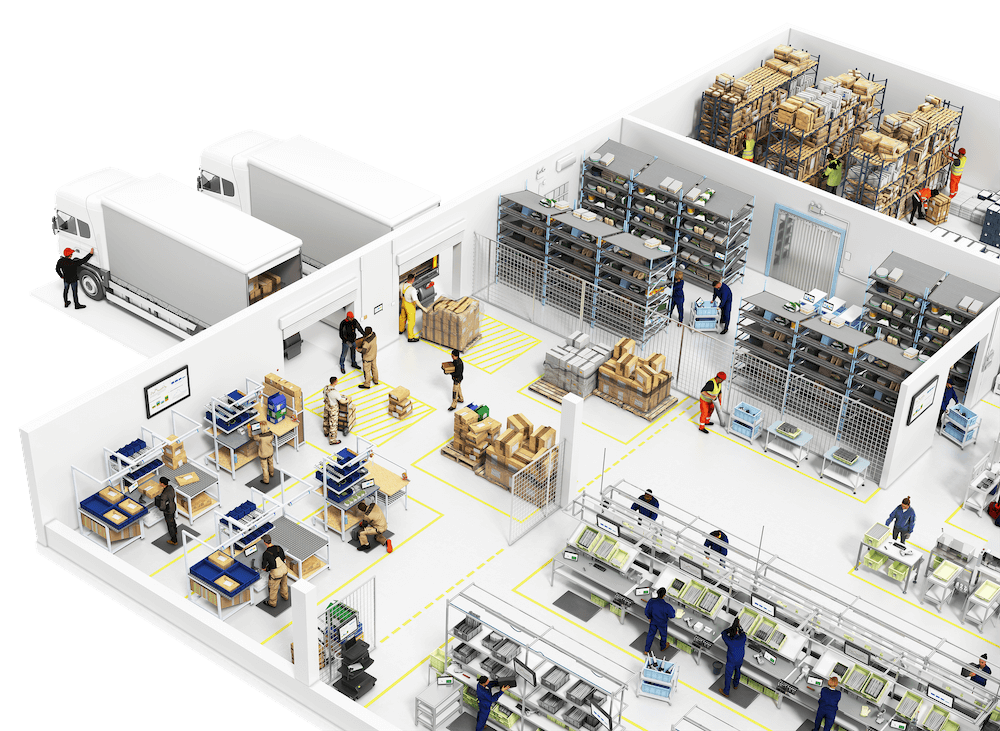