The importance of traceability in manufacturing has been well established. From root cause analysis to quality improvements and transparency boosting, traceability provides valuable insights into your plant's performance at any time for any station–a significant advantage when manufacturers are combatting fluctuations and uncertainties. Yet, traceability developments continue to lag behind other digital transformation efforts. Only 15% of manufacturers surveyed by the World Economic Forum in 2021 had made progress in investing in and scaling traceability technologies, and compliance remains the top goal for traceability initiatives.
These numbers raise a question: What is holding back progress and preventing manufacturers from turning traceability into their competitive advantage? The answer is how manufacturers are building and implementing their traceability systems.
The traditional traceability systems
The traditional approach to manufacturing traceability has focused on building an end-to-end system to gain full visibility of the production line. This is how it usually plays out:
you do your homework to understand the importance of having full traceability
you start designing your traceability systems with your engineering team or a third-party vendor
then you start your implementation plan
you hit a major roadblock: your end-to-end, large-scale systems are too costly and time-consuming to implement.
End-to-end visibility is great on paper, but impossible to achieve immediately without major disruptions and risks.
There are four main methods of managing manufacturing traceability: paper-based, ERP, MES, or home-grown solutions. These systems all suffer from one of these two issues: low returns or low adoption. Paper-based systems are unreliable and prone to human error. ERP systems have historically underdelivered despite the huge investments poured into this technology. MES are expensive and time-consuming to implement, and are rigid, all-or-nothing investments with no room for scaling or adjustments. Homegrown systems are hard to manage, and often single-threaded, creating tribal knowledge experts and preventing plant-wise adoption.
Unrealistic expectations and bad implementation are why 22% of manufacturers get stuck at the beginning of the journey in the strategizing phase. To break through, manufacturers need a different approach to building end-to-end traceability that can bypass the implementation hurdle and drive sticky changes in the operations.
Rethinking traceability in human-centric operations
The pitfall of the traditional approach is aiming for the instant achievement of full traceability. The scale and complexity of such a project introduce too many disruptions and risks to your existing processes and infrastructure, creating rich soil for chaos, waste, and changes that simply do not stick.
To avoid this pitfall, manufacturers need to start thinking in increments instead of going for an overhaul of the entire system, and gradually building up their coverage until they reach end-to-end traceability. This is the principle behind the agile implementation approach in manufacturing.
An agile approach allows manufacturers to quickly identify and resolve problems as they arise, by implementing short, inexpensive pilots at a time that targets those specific challenges. Each pilot represents a cycle of establishing goals, gathering the proper team, implementing sprints, and iterating and improving. Depending on the problems being tested, ROI can be seen within days or weeks.
Following an agile approach, the first step in building your traceability system is identifying the most critical pain points in your operations based on ease of implementation and business impacts. Your low hanging fruits are those with high business impacts and easy implementation. Whether it is parts tracking or quality monitoring, build an app to solve that one problem only and ensure that your workers are fully empowered to own the technology. Some questions to be answered at this stage include:
What data should you collect? Do you need more information about your products or processes?
What operational challenges does it point to?
Should you address this challenge now? Will it have a direct and immediate impact on your operations?
Start small with a few stations, then roll out the new apps and collect feedback from frontline workers. Use that feedback to inform your implementation and expand that suite of apps to solve the next problem in your operations. Bidirectional communication ensures a sticky adoption of your apps and prevents single-threaded operations. Instead of having one expert who runs every app, now you have a team of fully empowered workers. They can comfortably run the app, use its data, and communicate with process engineers to make real-time decisions, such as updating work instructions or quality control.
The mantra is building upon what you already have to drive continuous improvements. Stop to review and strategize after each app deployment. Use what you have already learned about your processes and your workers to inform the next extension. Make sure to involve your entire team from operators to engineers and plant managers in the problem-solving process. The key to driving sustainable changes is to ensure your technology solves a valid, tangible problem and make your workers’ life easier, not harder. Technology implementation should fit the requirements of your workforce, not the other way around.
There is no fixed way to do traceability–each organization is unique in its processes and challenges. Agile implementation will allow you to build your traceability systematically without straining your infrastructure or workforce and still see immediate value from your investment. Don’t get stuck chasing the elusive end-to-end traceability. It is something to be built, not found.
Turn traceability into your competitive advantage with Tulip
Learn how Tulip's Frontline Operations Platform enables agile implementation and helps you scale your traceability system
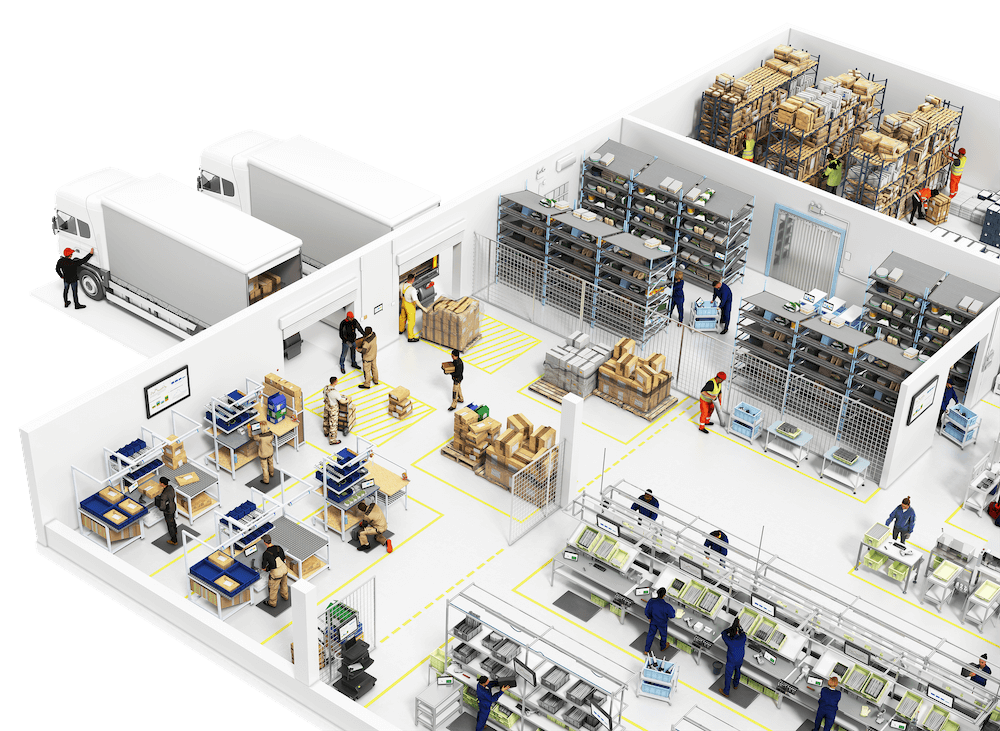