Was ist eine intelligente Fabrik?
Die Smart Factory ist ein Konzept, das das Endziel der Digitalisierung in der Fertigung zum Ausdruck bringt.
So wie der Begriff am häufigsten verwendet wird, handelt es sich bei einer Smart Factory um eine hochgradig digitalisierte Produktionsstätte, die über vernetzte Maschinen, Geräte und Produktionssysteme kontinuierlich Daten sammelt und austauscht. Die Daten können dann von selbstoptimierenden Geräten oder unternehmensweit genutzt werden, um proaktiv Probleme anzugehen, Fertigungsprozesse zu verbessern und auf neue Anforderungen zu reagieren.
Verschiedene Technologien wie KI, Big Data Analytics, Cloud Computing und Industrial IoT (Internet der Dinge) haben die Praktiken der intelligenten Fertigung umfassend gemacht.
Durch die Verbindung von physischer und digitaler Welt können intelligente Fabriken den gesamten Produktionsprozess überwachen, von den Fertigungswerkzeugen und der Lieferkette bis hin zu den einzelnen Mitarbeitern in der Werkstatt.
Wenn sie vollständig realisiert sind, nutzen intelligente Fabriken vollständig integrierte, kollaborative Fertigungssysteme, um den Betrieb flexibel, anpassungsfähig und optimierbar zu machen.
Technologien der Industrie 4.0 in der intelligenten Fabrik
Die von intelligenten Fabriken angewandte Fertigungspraxis - Smart Manufacturing - ist die optimalste Anwendung von Technologien, die aus der vierten industriellen Revolution, bekannt als Industrie 4.0, hervorgegangen sind.
Bei der intelligenten Fabrik geht es nicht darum, eine Software in der gesamten Fertigung einzusetzen und sofortige Verbesserungen im Produktionsprozess zu sehen. Eine Kombination aus verschiedenen Industrie 4.0-Technologien trägt zur Optimierung der intelligenten Fertigung bei. Hier sind die wichtigsten Grundlagentechnologien:
Industrie IoT (IIoT)
Industrie IoT bezieht sich auf miteinander verbundene Geräte, Maschinen und/oder Prozesse, die durch Datenkommunikationssysteme miteinander verbunden sind, um den Austausch und die Nutzung von Daten zwischen Menschen und Maschinen zu erleichtern. In der Regel verfügen diese Geräte über Sensoren, die aussagekräftige Datenpunkte in einer Cloud oder einer Offline-Datenbank sammeln, um den Herstellungsprozess zu verfolgen und Verbesserungsmöglichkeiten aufzuzeigen. Industrial IoT ermöglicht betriebliche Effizienz, Kontrolle und Einsicht in umsetzbare Schlüsselmetriken.
Sensoren
Sensoren, die an Geräten und Maschinen angebracht sind, helfen bei der Erfassung bestimmter Datenpunkte in bestimmten Phasen des Herstellungsprozesses und bieten so sofortigen Einblick in die verschiedenen Ebenen der Produktion. Zum Beispiel können Temperatursensoren in einem Reinraum das Klima in einem Labor verfolgen und erkennen und diese Daten über ein IoT Gateway weitergeben. Die Daten können dann zur Selbstkorrektur mit KI (Künstliche Intelligenz) verwendet werden oder die zuständigen Teammitglieder zur Überprüfung alarmieren.
Cloud Computing
Cloud Computing ermöglicht intelligenten Fabriken die Speicherung, Verarbeitung und gemeinsame Nutzung von Daten mit größerer Flexibilität und zu geringeren Kosten als herkömmliche Vor-Ort-Alternativen. Vernetzte Geräte und Maschinen in der Fertigung profitieren davon, dass sie schnell große Datenmengen hochladen können, die dann für Feedback und Entscheidungen nahezu in Echtzeit ausgewertet werden können.
Big Data-Analytik
Die Anhäufung von Daten im Laufe der Zeit kann Aufschluss darüber geben, wie effizient der Produktionsprozess ist, auf welche Schlüsselkennzahlen man sich konzentrieren sollte und welche Systeme unterdurchschnittliche Leistungen erbringen. Die schiere Größe von Big Data kann Fehlermuster aufdecken und eine vorausschauende Qualitätssicherung mit hoher Genauigkeit durchführen. Die Präsentation und das Timing von Big Data-Analysen - die Bereitstellung der richtigen Informationen zur richtigen Zeit - ermöglicht es den Betrieben, sich optimal und schnell zu verbessern.
Vorteile der Smart Factory
Intelligente Fabriken optimieren die Effizienz und Produktivität, indem sie die Fähigkeiten von Produktionsgeräten und Menschen erweitern. Indem sie sich auf die Schaffung eines agilen, iterativen Produktionsprozesses durch Datenerfassung konzentrieren, können smarte Fabriken Entscheidungsprozesse mit stärkeren Beweisen unterstützen.
Durch die kontinuierliche Verbesserung der Produktivität von Fertigungsprozessen können intelligente Fabriken Kosten senken, Ausfallzeiten reduzieren und Verschwendung minimieren. Das Erkennen und Reduzieren von fehlgeleiteten oder nicht ausgelasteten Produktionskapazitäten bedeutet Wachstumschancen ohne Investitionen in zusätzliche finanzielle und/oder physische Ressourcen.
Smart Levels: Vier Levels der Smart Factory
Diese vier Stufen von Datenstruktur können Ihnen dabei helfen zu beurteilen, wo Sie sich auf dem Weg zu einer intelligenten Fabrik befinden und welche Schritte Sie unternehmen müssen, um die nächste Stufe zu erreichen.
Ebene Eins: Verfügbare Daten
Dies ist wahrscheinlich der aktuelle Status der meisten Fabriken. Daten sind zwar vorhanden, aber nicht zugänglich. Das Sortieren und Analysieren von Daten erfordert manuelle Arbeit und kann sehr zeitaufwendig sein, was den Prozess der Produktionsverbesserung ineffizienter macht als beabsichtigt oder nötig.
Ebene Zwei: Zugängliche Daten
In diesem Stadium werden die Daten in einer besser verdaulichen Form präsentiert. Die Daten sind strukturell organisiert und an einem Ort richtig sortiert. Zusätzliche Systeme helfen bei der Visualisierung der Daten und der Anzeige von Dashboards. Die Fabrik ist in der Lage, proaktive Analysen durchzuführen, auch wenn dies noch etwas Zeit und Mühe erfordert.
Stufe 3: Aktive Daten
Aktive Daten sind Daten, die mit Hilfe von machine learning und künstlicher Intelligenz proaktiv analysiert werden können, um ohne viel menschliche Aufsicht Erkenntnisse zu gewinnen. Das System kann wichtige Probleme und Anomalien erkennen, um Ausfälle mit hoher Genauigkeit vorherzusagen und die zuständigen Personen zum richtigen Zeitpunkt mit wertvollen Erkenntnissen zu informieren.
Ebene Vier: Handlungsorientierte Daten
In dieser Phase kann machine learning umsetzbare Lösungen für die Probleme generieren, die in den früheren Phasen identifiziert wurden. Die Produktionsmaschinen und -geräte, die mit diesem Modul oder System verbunden sind, können diese Änderungen dann ohne menschliches Zutun ausführen. Das Sammeln von Daten, das Erkennen von Problemen und das Generieren von Lösungen geschieht nacheinander und mit wenig bis gar keinem menschlichen Zutun.
Digitalisieren Sie Ihre Produktionsstätte mit Tulip
Erfahren Sie, wie Sie die Datenerfassung von Menschen, Maschinen und Sensoren in Ihrem Betrieb digitalisieren können.
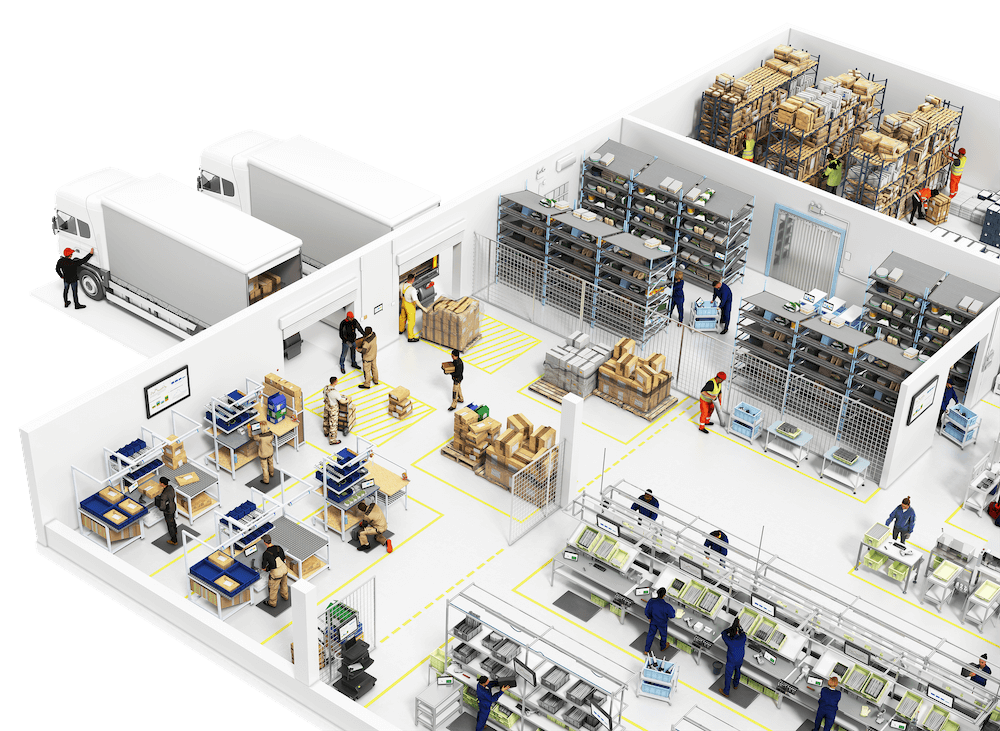